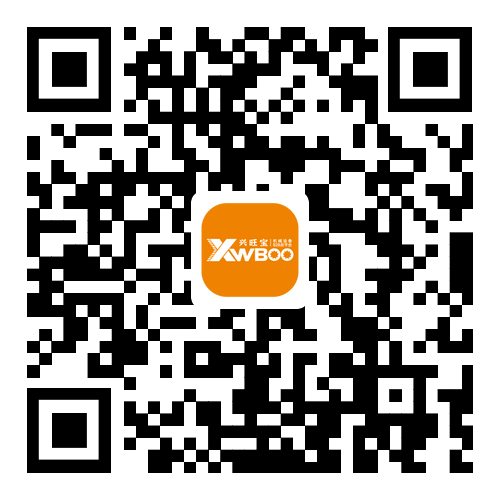
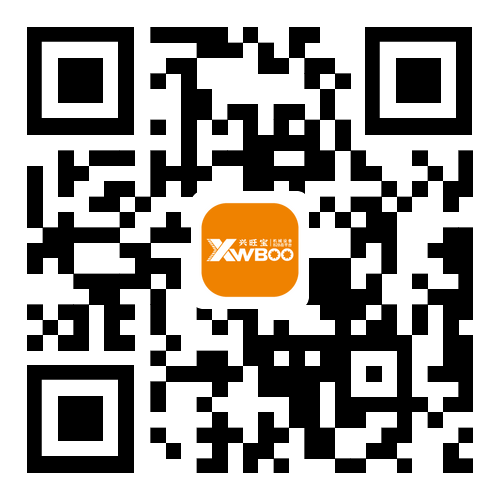
产品详情
● 火力发电行业为什么要进行锅炉烟气综合治理 |
随着经济和社会的发展,环境污染问题日益严重,火力发电行业是环境污染的主要源头。关键在锅炉烟气危害较大,烟气中包括粉尘、二氧化硫及氮氧化合物等,对环境以及对人体健康都会造成危害。 煤炭燃料在锅炉内燃烧过程中除放出大量热量外,还会产生大量烟尘。烟尘由气体和固体两部分组成。气体部分主要有二氧化碳、一氧化碳、水蒸气、氮气、氧气、氧化氮、二氧化硫和硫化氢,固体部分主要是飞灰和炭黑。 炭黑是煤中挥发物质在高温缺氧的条件下热分解的产物。炭黑颗粒粒径细微,能在空气中漂浮很长时间,形成黑烟。由于炭黑是燃烧不的产物,烟气中还混有未燃尽的碳粒,随着烟气排人大气中。由于尘粒粒径不同,在重力作用下其沉降特性也不同。粒径小的尘粒可以长期漂浮在空中,称为飘尘。粒径大的颗粒能较快的沉降,称为降尘。工业锅炉排出的烟尘中的尘粒吸附能力很强,很多有害气体和液体能吸附在这些微粒上而被吸人人体内,粘附于支气管壁和肺泡壁上,危害人们的身体健康。烟尘能够使植物的光合作用减弱,造成植物叶片枯萎,使农作物产量降低。 烟气中的二氧化硫是一种无色有臭味的气体。当大气中的二氧化硫浓度达到3.5mg/m3时,会使人的呼吸系统、心血管系统疾病的发病率和死亡率增加,它还会腐蚀工业设备和构筑物,更严重的会形成酸雨、破坏植被、森林平衡。烟气中的一氧化氮和一氧化碳等有害气体,被吸人人体后,会使人缺氧而麻痹。 总之,燃料在锅炉内燃烧后产生大量的烟尘、硫和氮的氧化物等有害气体,这些有害物质排放到大气中,对人们的生产、生活、健康以及环境都会造成极大危害。对此,要要引起高度重视,加强对电厂锅炉烟气的处理对于改变我国的空气环境具有着重要的意义,天洁公司主要对电厂锅炉烟气净化综合治理技术进行深入的研究和对项目的治理实施。 |
● 锅炉除尘设备产品简介 |
天洁产品:节能省耗 绿色环保 天洁产品研发体系,凭借天洁人的设计研发能力、国际标准的制造工艺、ISO的质控管理体系,已经发展到新的高度,可根据每个用户的具体需求或项目的特色,进行个性化研发设计,为其量身定制大气净化产品,节约成本,实现节能省耗,减少污染,绿色环保的可持续发展。 锅炉除尘器详细介绍 常见的锅炉除尘设备中有机械力除尘器、电力除尘器、布袋过滤除尘器、洗涤除尘器,它们是按照除尘器的作用原理来进行分类的。 因为锅炉中的燃料在燃烧的过程中会产生大量烟气(其中气相物质和固相物质混合在一起)。这样就会使锅炉发生堵塞的现象,所以需要做除尘处理。 为了减少和控制锅炉烟尘的排放对环境产生的危害,我们国家已经制订出了《锅炉(不含电站锅炉)烟尘排放标准》的规定。这样就需要对工业上使用的锅炉进行改造,对烟尘进行治理。 锅炉除尘设备特点 锅炉除尘设备是在布袋除尘器的基础上,改进的新型锅炉除尘设备。为了进一步完善锅炉除尘器,净化效率高,处理气体能力大,性能稳定,操作方便、滤袋寿命长、维修工作量小等优点。而且从结构上和电磁脉冲阀上 进行改变,解决了露天安放和压缩空气压力低的问题。适用机械、冶金、橡胶、面粉、化工、制药、碳素、建材、矿山等单位。 燃煤锅炉布袋除尘器设计选型依据袋式除尘器设计选型通常依据处理风量来确定设备规格,结合入口粉尘浓度并按照设备阻力要求选择过滤风速,结合烟气温度、湿度、气体组分、粉尘特性、排放要求来确定滤袋材质及表面处理方式,并根据入口粉尘浓度、粉尘颗粒度来确定除尘器的结构型式,包括除尘器进风方式、烟气流场分布和清灰方式。 过滤风速也称气布比,通常在入口粉尘浓度小于50g/Nm3条件下,适合的过滤风速选择在0.9-1.0m/min,在入口粉尘浓度在50-100g/Nm3条件下,适合的过滤风速选择在0.85-0.9m/min。选择好过滤风速后,即可结合处理烟气量确定过滤面积。按此进行设计选型,设备运行阻力可以控制在1200Pa以下。 燃煤锅炉烟气进入到燃煤锅炉布袋除尘器入口温度通常在120-160℃之间,也有少量运行温度小于110℃或大于170℃,尽管很多高温滤料单纯从滤料耐温角度而言是可以选择的,但由于烟气中存在O2、NO2、SO3、H2O等物质,这些物质对某些滤料在高温条件是有化学损伤作用的,因而滤料选择要结合温度、烟气组分和性价比综合考虑。 烟气湿度是影响烟气露点温度的重要因素之一,也会影响到粉尘的黏度,从而影响到除尘器的过滤和清灰性能。锅炉爆管导致大量水汽进入除尘器进而产生糊袋现象,就是烟气湿度急剧升高原因所致。有些燃料如褐煤、煤泥含水率高达30%,烟气湿度对应要达到12-15%,比常规的烟气湿度5-8%要高出一倍以上,势必使粉尘的黏性加大,此时滤料的表面处理就至关重要,除常规的烧毛、热定型外,还需进行PTFE乳液浸渍处理,目的就是提高滤料表面的易清灰性能。同时,高的烟气湿度在温度较高的条件下,对P84、NOMEX等滤料具有一定的水解损伤作用。 烟气组分中的O2、NO2、SO3对滤料具有较强的氧化作用,而SO2、SO3、HCl、HF又对滤料具有较强的酸腐蚀作用,燃煤中的这些对滤料容易造成化学损伤的物质不可避免的存在,因而在滤料材质选择方面就需要考虑这些因素,而且这些物质在烟气中所占的比例和烟气运行温度一同影响着滤料材质的选择。 粉尘的特性决定着滤袋的表面处理方式和清灰方式,其特性表现在粒径分布、粉尘形状、粉尘的密度、附着性和凝聚性、吸湿性和潮解性、磨啄性。粉尘的粒径分布主要影响袋式除尘器的清灰和阻力,细颗粒粉尘难捕集,捕集后的形成的粉尘层较密实,对清灰会造成一定的困难,粗颗粒粉尘易捕集,捕集后形成的粉尘层较疏松,有利于清灰,但粗颗粒粉尘对滤料和设备都有一定的磨损作用,特别是粉煤灰磨啄性很强,覆膜滤袋不适合在此工况条件下使用。从某种意义上讲,粗细搭配的混合粉尘对过滤和清灰都是有利的。粉尘形状分为规则形和不规则形,规则形粉尘表面光滑,比表面积小,不容易被滤料拦截,不规则形粉尘表面粗糙,比表面积大,容易被滤料拦截。但不规则形状的尘粒容易对滤袋产生磨损。对于多数粉尘而言,其密度对袋式除尘器的设计选型影响不大,但是,密度特别小的粉尘将对清灰增加困难,需要特别考虑气流分布和清灰方式。粉尘的附着性和凝聚性有利于微细粉尘的凝聚和一次粉尘层的建立,从而提高除尘效率,但不利于清灰。吸湿性和潮解性强的粉尘极易在滤袋表面吸湿和固化,有些粉尘吸湿后发生潮解,其性质和形态均发生变化,形成粘稠状物,将导致除尘器清灰困难,阻力增大。粉尘的磨啄性关系到除尘器本体设计和进风方式的选择,甚至要考虑预处理措施,局部流速高的部位要做防磨处理。 3、燃煤锅炉布袋除尘器结构设计袋式除尘器是利用纤维编织的袋式过滤元件来捕集含尘气体中固体颗粒物的除尘装置。其过滤机理是尘粒在绕过滤布纤维时因惯性力作用与纤维碰撞而被拦截。细微的尘粒(粒径为1?m或更小)则受气体分子冲击(布朗运动)不断改变着运动方向,由于纤维间的空隙小于气体分子布朗运动的自由路径,尘粒便与纤维碰撞接触而被分离出来。过滤的过程分两个阶段,首先是含尘气体通过清洁的滤料,此时起过滤作用的主要是滤料纤维的阻留;其次,当被阻留的粉尘不断增加,一部分粉尘嵌入到滤料的内部,一部分覆盖在滤料表面形成粉尘层,此时主要靠粉尘层过滤含尘气体。随着燃煤锅炉布袋除尘器过滤工作的延续,除尘器滤袋表面的粉尘将越积越厚,直接导致除尘器阻力的上升,因此,需要对滤袋表面的粉尘进行定期的清理,即清灰。 3.1烟气流场分布设计 燃煤锅炉布袋除尘器从其除尘机理而言,保证达到预期的排放指标是很容易实现的,但如何保证滤袋使用寿命更长,达到30000小时的保证寿命甚至更长,至关重要的因素之一即是创建合理的烟气流场,也就是促使气流均匀分布到每个过滤单元和每条滤袋。气流扩散空间大有利于烟气的自然分配,同时烟气由于速度低,该空间兼有重力除尘功能,如果在进风口或扩散区域设置导流板,除有利于气流分布外,还可以兼有惯性除尘作用,这样可以大幅度降低接触到滤袋的烟尘浓度。尤其是高含尘浓度、粉尘颗粒较粗的工况条件更应考虑这样的设计原则,如干法脱硫后、煤矸石电厂和其它燃烧劣质煤的工况。 袋式除尘器气流分布主要决定于进风方式的选择与设计。从进风方式来看,袋式除尘器的进风方式有单元进风、沉降进风、直通进风、阶梯进风等多种方式,各种进风方式均有其各自的优缺点,但从降低设备固有阻力来看,直通进风和阶梯进风方式相对比较合理,从离线清灰和不停机检修来看,单元进风和沉降进风方式更具有性。 单元进风方式的袋式除尘器由若干个单元仓室(3-24个)组合而成,通过进出口总管将单元进出风口连接,设计时要求充分考虑进风总管与各支管的流量分配和阻力分布情况,合理选择气流速度,合理设置均风导流装置,促使烟气能够在各仓室等量分布,各滤袋承受负荷均匀,以达到降低设备阻力和延长滤袋使用寿命的目的,从而保证设备能够长期稳定可靠、经济的运行。 沉降进风方式与单元进风方式类似,同样由若干个单元仓室(3-24个)组合而成,通过进出口总管将单元进出风口连接,区别在于单元进风口竖直向下,而不是水平接入单元灰斗,这样设置方式可以起到惯性除尘的作用,尤其适用于高粉尘浓度场合的除尘,如干法脱硫后配套的袋式除尘器。 直通进风方式为除尘器采用箱体扩散进风,来自空预器的烟气通过烟道进入到除尘器的进口喇叭,进口喇叭内部设置有两级布风板,烟气经布风板和导流板分配后进入袋滤区域,袋滤区内安装有滤袋和笼骨,烟气透过滤袋完成了过滤,粉尘被阻挡在滤袋的外表面,过滤后的洁净气体在滤袋内部,并通过排风总管排放。 阶梯式进风方式同样采用箱体扩散进风,来自空预器的烟气通过烟道进入到除尘器的进口喇叭,进口喇叭内部设置有两级布风板,布风板上按规则开孔,二级布风板放置在进口喇叭末端,与顶板相连,与两侧壁板、灰斗上沿均留有一定的距离,实现孔内进风占总烟气量的1/6、侧面进风占总烟气量的1/3、底面进风占总烟气量的1/2的三维布风方式,并结合滤袋的阶梯形排布,实现在进风方向上,呈流通面积阶梯递减趋势,在出风方向上,呈流通面积阶梯递增趋势。为保证出风顺畅,避免气流积聚,在出口喇叭内设置纵横两向交错的导流叶片,形成分层网锥出风。 检验烟气流场设计合理与否可以通过三种方式加以评判。一是通过数学建模,即通过CFD模拟方式判断烟气流场中各点的烟气流速是否符合设计要求。二是通过建立物理模型,按实际所需设备规格的10-20%比例并依据相应的方法创建模型,风机开启后借助风速仪检测除尘器各区域的烟气流速,在此过程中可以适当调整导流板的方位。三是通过现场冷态启动风机在净气室内测试各区域袋口的过滤风速,如果各袋口出风速度均匀,可以判定整个烟气流场符合技术要求。 3.2燃煤锅炉布袋除尘器清灰系统设计 袋式除尘器的清灰系统设计及清灰制度的设置合理与否将直接影响到除尘器的运行稳定性及滤袋的使用寿命。对袋式除尘器的清灰来说,清灰太不行,因为这样会失去粉尘层的过滤作用,更多的超细粉尘会直接进入滤料内部而引起过滤阻力不断上升,以及清灰力过大会影响滤袋寿命等。清灰不也不行,这样会使滤袋的过滤阻力过高,而影响整个机组的正常运行。另外,袋式除尘器的清灰还要尽可能地保证整个滤袋及各个区域清灰程度均匀,否则会引起整个系统阻力分布不均匀,从而影响到内部的气流分布。 袋式除尘器的清灰很多,从目前我国燃煤电厂已投入商业化运行的袋式除尘器来看,清灰方式主要分为低压脉冲固定行喷吹方式、低压脉冲旋转喷吹方式和分室定位反吹方式,其中前两种应用更为普遍一些。 低压脉冲固定行喷吹袋式除尘器的脉冲喷吹装置采用固定管喷式结构,一只脉冲阀对应一根喷吹管,而一根喷吹管对应14-16个喷嘴,喷嘴孔径大小不一,呈规则排布,并与滤袋逐一对应,脉冲阀开启时间为0.1秒,补气时间为10秒。电磁脉冲阀采用进口产品,喷吹压力为0.2~0.3MPa(可调),气量为0.2~0.25m3/次。低压脉冲固定行喷吹袋式除尘器喷吹清灰原理是依靠脉冲阀膜片快速开启,在瞬间释放压缩空气,压气从喷嘴中高速喷出,引射数倍的周围气体注入袋内,滤袋快速膨胀,袋壁产生很大的加速度,抖落滤饼,从而实现清灰。 低压脉冲旋转喷吹袋式除尘器每个滤袋束设置一个清灰装置,其中包括一个脉冲压缩空气储气罐,电磁隔膜阀和旋转支管。脉冲清灰压缩空气由罗茨风机提供。罗茨风机将压缩空气通过输气管道输送到位于除尘器顶盖上部的压缩空气储气罐中,当清灰指令下达以后,压缩空气从储气罐经过隔膜阀和旋转风管将压缩空气喷入滤袋实现脉冲清灰。旋转风管在花板上部分为3-6个支管,在旋转风管的底部有一个密封轴承支座。在每一圈布袋上都对应若干个数量不等的喷嘴,旋转风管通过法兰与支管连接,旋转风管穿过净气室顶部,旋转风管通过齿轮传动装置由马达驱动,转速约为1转/分。 分室定位反吹袋式除尘器采用锅炉引风机出口的净化烟气作为清灰气源,通过反吹风机、回转定位反吹装置反吹到滤袋内部,风量为总风量的1%左右,风压为3000Pa。 三种清灰方式比较分析如下: 3.2.1低压脉冲固定行喷吹袋式除尘器清灰方式 每个喷嘴与滤袋一一对应,清灰比较,且喷吹系统没有运转部件,因而运行稳定可靠; 脉冲阀数量较多,通常为3”,每只脉冲阀对应的滤袋面积一般小于60㎡,因而个别脉冲阀出现故障,对除尘器总体运行性能影响不大; 采用圆形滤袋并呈矩形布置,各滤袋表面承受含尘气体压力相同,有利于滤袋寿命的保证; 采用的单仓过滤面积一般为600-1500㎡左右,仓室数量可灵活调整,对场地的适应性很好,更容易实现离线清灰和不停机检修。 3.2.2低压脉冲旋转喷吹袋式除尘器清灰方式 旋转支管底部的喷嘴对应滤袋束进行喷吹,边吹边旋转,喷吹气量较大,压力较小,喷吹下来的压缩空气并不能直接射入到滤袋内部,部分空气吹到花板或滤袋边缘,清灰并不; 脉冲阀数量较少,通常为8-12”,每只脉冲阀对应的滤袋面积一般小于1500-2500m2,因而个别脉冲阀出现故障,对除尘器总体运行性能影响较大; 因采用旋转喷吹方式,滤袋通常为扁圆形,呈同心圆布置。滤袋排布紧密但仓室四角闲置。 单仓过滤面积较大,如果单仓离线检修时,将使除尘器过滤风速形成较大幅度的增加,为了保证滤袋的使用寿命和避免除尘器阻力的过分增大,单仓检修时一般需要锅炉减负荷运行。 3.2.3分室定位反吹袋式除尘器清灰方式 采用锅炉引风机出口的净化烟气作为清灰气源,与除尘器内的烟气等温、等氧含量,可避免温差和氧量增加对滤袋的影响,但应防止粉尘排放超标现象,否则会出现“倒灌灰”现象; 回转定位反吹装置对应滤袋束进行吹扫,吹扫气量很大,压力很小,吹扫下来的净化烟气并不能直接射入到滤袋内部,部分吹到吹到花板或滤袋边缘,清灰并不; 回转定位反吹装置因有转动机构,存在一定的故障隐患。 综上所述,低压脉冲固定行喷吹方式清灰更为,且没有转动机构,更能满足电厂运行稳定可靠的要求。 3.3燃煤锅炉布袋除尘器保护系统设计 保护系统是依据锅炉启停和出现异常情况时烟气工况条件设计的。主要由预涂灰装置、紧急喷淋降温系统、旁路系统、滤袋保护装置等组成。 预涂灰包括投运前对滤袋表面形成粉尘层、长时间低负荷全投油运行和长时间停炉再次启动三种情形,特别是有些电厂位于城区附近,在锅炉启动投油和低负荷投油助燃时由于环保要求不允许开旁路,而直接要经过滤袋,如滤袋不采用预涂灰,必将导致滤袋出现油雾堵塞现象。 紧急喷淋降温系统是针对锅炉结焦、换热器出现故障等排烟温度超过滤料所能承受的极限温度时设置的,采用两级喷淋形式,喷嘴为气液两相雾化结构,降温效果不小于30℃。 旁路系统是针对锅炉“四管”爆裂导致烟气湿度大幅度增加或锅炉过度超温而紧急喷淋降温系统也无法降下来时设置的,旁路阀门采用气动提升双阀门结构型式,保证零泄漏。 滤袋保护装置包括检露和糊袋、堵袋检测,每个单元仓室设置浊度仪和差压变送器。浊度仪检测单元仓室排放浓度达到设定值时报警,从而检查判断滤袋是否出现破损;差压变送器检测滤袋过滤阻力达到设定值时报警,从而检查判断滤袋是否出现糊袋、堵袋。 4、滤袋的选型及注意事项滤袋和笼骨组成了袋式除尘器的过滤系统,对于整台锅炉袋式除尘器而言,滤袋是其核心部件。滤料质量直接影响除尘器的除尘效率,滤袋的寿命又直接影响到除尘器的运行费用。因而,通常滤料需要根据除尘器运行环境和介质情况选用合适的材质。电站除尘器常见到的滤料有PPS,P84,PTFE等,常用的是PPS,克重550g/m2,通常采用烧毛、热定型处理,如果含湿量≥10%,或含氧量≥10%且温度大于160度,需另进行PTFE浸渍处理,以提高抗水解和抗氧化性能。如果运行温度长期在190℃以上,应考虑采用纯PTFE滤料。P84因易水解,不宜在燃煤锅炉袋式除尘器中单独使用,但可以用PPS +P84针刺毡复合刺毡,通常P84含量为10-15%,主要为了进一步提高过滤精度,其它性能不发生改变,布袋成本也稍高一些。由于电厂粉煤灰中二氧化硅、三氧化二铝含量高,在清灰过程中对覆膜滤料表面的膜容易产生磨损,进而出现膜脱落现象,覆膜滤料不适用于燃煤锅炉烟尘的处理。 5、滤袋的失效与解决方案滤袋在袋式除尘器的投资和维护费用中所占的比例都是相当大的,约占投资费用的比例为30%,占维护费用的比例为80%以上,因而如何避免滤袋过早失效是降低除尘器维护费用的重要途径。 燃煤电厂滤袋的失效分为物理失效和化学失效两种,而物理失效包括机械磨损、烟气冲刷、堵塞失效三种类型,化学失效包括高温损伤、酸碱腐蚀和氧化腐蚀。 ①机械磨损 机械磨损与袋式除尘器的加工、运输、安装及钢结构设计有关,常见的有:袋笼的外径偏小、竖筋数量偏少、横筋间距偏大而导致滤袋与袋笼之间形成挤压力,将滤袋撑破;运输和安装过程中由于不慎产生划伤;喷吹管上的喷嘴与花板孔之间同心度达不到要求或喷嘴与花板之间垂直度不够而导致喷吹过程中压缩空气直接吹到滤袋袋身上,造成了滤袋局部受冲击过大而破损;袋笼表面有毛刺、凸起或两节连接处脱开导致在过滤和清灰往复过程中对滤袋的间歇性磨损;滤袋和花板配合不好如滤袋袋口没有展开或袋口与花板存有间隙出现“跑灰”现象,导致粉尘冲刷袋口;花板有缺口或凹凸、滤袋接缝不规范也会出现“跑灰”现象;滤袋与壁板上的加强型钢或残留的吊耳相接触,滤袋因花板平整度不够或袋笼垂直度不够,都将导致清灰过程中滤袋的摆动造成撞击磨损。 解决方案:设计、加工、运输、安装过程中应精心化组织,配套件质量应严格把关,在除尘器投运前应进行的检查,尽可能减小现场安装工作量,并配备相关的设施,将质量较高要求的尽可能由生产车间完成。 ②烟气冲刷 烟气冲刷与除尘器结构设计有关,主要是由于烟气到达滤袋的流速太高,烟气携带粉尘直接冲刷滤袋导致滤袋磨损,特别是高含尘浓度工况或除尘器进风通道出现积灰时,这一现象会更加容易发生。采用下进风方式的除尘器磨损的部位通常在滤袋的底部,采用水平进风方式的除尘器磨损的部位通常在前排滤袋,尽管滤袋底部采用了加厚层,但也无法从根本上避免这一问题。 解决方案:建立合理的烟气流场,采取必要的导流、均流措施,采用多方位进风方式,形成烟气蔓延整个过滤区域的趋势,确保烟气到达滤袋时的风速小于1m/s,同时应避免除尘器进风通道出现积灰和灰斗输灰不畅引发的灰位过高现象发生。 ③堵塞失效 堵塞失效主要包括粉尘堵塞、油雾堵塞、结露糊袋三种类型。粉尘堵塞主要是由于清灰不够引起的,特别是锅炉低负荷时除尘器长时间不清灰也会导致这一问题的出现,微细的粉尘游弋于滤袋的表面,在过滤过程中由于粉尘之间的挤压导致粉尘浸透到滤袋纤维夹层中,引起滤袋局部固有阻力的增加,整条滤袋透气的均匀性发生了改变,这不仅会引起除尘器运行阻力的增加,还会改变烟气的过滤路径,增加未曾堵塞的滤袋部位的过滤负荷,加剧了滤袋状况的恶化;油雾堵塞主要是锅炉启动或低负荷运行投油助燃时未对滤袋采取保护措施或保护措施不到位引起的,这会导致滤袋的固有阻力增加,即便采用强力清灰也难以解决这一问题;结露糊袋主要是除尘器低于酸露点运行,凝结的酸附着在滤袋外表面,这种现象主要出现在锅炉启动是烟温过低或锅炉出现大面积爆管时,结露糊袋同样会导致滤袋的固有阻力增加,还可能同时导致酸对滤袋的腐蚀。 解决方案:选择合理的清灰系统结构型式,设置合理的清灰压力、清灰周期和清灰控制方式,以保证清灰相对,避免粉尘堵塞现象发生,特别注意的是,过度清灰也不可取,这是因为过度清灰会影响滤袋的使用寿命和过滤性能;除尘器投运前应对滤袋进行预涂灰,事先在滤袋表面形成粉尘层,可以实现粉尘层对油雾、酸的包裹阻拦,避免油雾、酸与滤袋表面的直接接触,避免油雾堵塞、结露糊袋现象的发生;当锅炉低负荷运行需投油助燃时,应调低清灰压力和清灰频次,使滤袋表面一直留有一定厚度的粉尘层,实现对滤袋的保护;当锅炉出现大面积爆管时,通过湿度监测仪判断湿度已经大于15%时,应考虑停炉或开启除尘器旁路。 ④高温损伤 高温损伤主要是高温尘粒对PPS滤袋表面的局部损伤。含尘气体携带着不同粒径的粉尘颗粒,冷却措施往往只达到对气体温度和微细颗粒的降温,由于气流速度较高及冷却空间有限,粗颗粒往往没有及时降温便进入除尘系统,高温粗颗粒在滤料表面被拦截并冷却,该温度下的颗粒一般为高温火星,造成滤料表面的局部热损伤。工程案例中往往碰到烟气温度满足滤料使用要求但滤料局部损伤的问题,其内在原理便是如此。因此,对高温烟气的降温固然重要,但对粗颗粒的预除尘也是不容忽视的。 ⑤酸碱腐蚀 燃煤电厂所采用的滤料通常为PPS针刺毡,滤料在应用中的化学腐蚀主要包括两种,一种是气体腐蚀,即烟气中的腐蚀性气体在高温条件下,与滤料发生缓慢的化学反应。而另一种是液体腐蚀,主要包括酸性腐蚀、碱性腐蚀和氧化性腐蚀。酸性腐蚀主要是指烟气含酸性气体浓度较高的条件下,烟气温度低于酸性气体的露点温度时,气体在滤料表面结露而腐蚀滤料。液体结露腐蚀易使滤料在短时间内产生表面结垢甚至堵塞,导致运行阻力过高,清灰性能失效,或造成滤袋破损,过滤性能失效,严重地将腐蚀除尘系统结构材料。同时,当烟气中水蒸气含量较高时,加速烟气中酸性物质的腐蚀作用,并对滤料的氧化水解也起到催化作用,使得滤料因强度大幅度下降而失效,进一步降低滤料的使用寿命。碱性腐蚀主要来自于烟尘灰份中、等物质,碱性物质易潮解,当烟气中水蒸气含量过高时,碱性物质易在滤料表面潮解而腐蚀滤料。 PPS纤维的耐化学品性能总体不错,但实际化工废气和各种炉窑中,烟气的成分很复杂,通常含有酸、碱、氧化剂、有机溶剂等多种化学成分,且处在高温、高湿条件下,对PPS滤料的腐蚀作用受多种因素的交叉影响。如果烟气中含有强氧化性化学品如Br2,或对PPS纤维影响较大的有机物质如甲苯,要先经过预处理,然后再通过PPS滤袋。 ⑥氧化腐蚀 滤料材质的耐温程度是有限的,因此含尘气体的温度对滤料性能是一个首要因素。当烟气温度过高时,除了滤料本身材质的强度会降低,烟气中的腐蚀性气体,如强氧化型气体也更容易与滤料发生化学反应,烟气中的氧和氮氧化物容易对滤料有氧化腐蚀作用,不仅可对滤料造成缓慢的腐蚀作用,也可直接造成滤料失效,影响滤料的使用寿命。例如,高温条件下,含氧量过高容易造成覆膜滤料的膜因高温氧化而脱落失效。应用中要保证锅炉稳定燃烧,烟气温度要控制在滤料使用温度范围内,减少滤料使用的瞬间高温的影响。据瑞典化学家Arrhenius发现的规律,温度每升高10℃,化学反应速度加倍。因此,在高温烟气进入除尘器之前一般行降温处理,使温度处于滤料的适宜应用条件。气体对滤料产生的缓慢腐蚀一般发生在高温的夏季。 |
● 锅炉烟气除尘 |
锅炉在使用的过程中不可避免地产生粉尘和烟气,锅炉烟气除尘就是把锅炉中的粉尘从烟气中分离出来,从而减少粉尘污染并且有利于进一步对烟气进行脱硫、脱硝等处理。随着社会的发展,环保越来越受到人们的重视,锅炉除尘也已经应用到火力发电等各个领域。锅炉除尘采用的除尘设备包括机械除尘器、袋式除尘器、电除尘器和湿除尘器等。但每种除尘净化系统总有其技术上的优点和缺点,应根据实际情况选择合适的除尘设施与工艺。![]() |
● 锅炉烟气脱硫 |
锅炉烟气脱硫,是指将煤中的硫元素用钙基等方法固定成为固体防止燃烧时生成SO2。通过对国内外脱硫技术以及国内电力行业引进脱硫工艺试点厂情况的分析研究,目前脱硫方法一般可划分为燃烧前脱硫、燃烧中脱硫和燃烧后脱硫等3类。其中燃烧后脱硫,又称烟气脱硫(简称FGD),在FGD技术中,按脱硫剂的种类划分,可分为以下五种方法:以CaCO3(石灰石)为基础的钙法,以MgO为基础的镁法,以Na2SO3为基础的钠法,以NH3为基础的氨法,以有机碱为基础的有机碱法。世界上普遍使用的商业化技术是钙法,所占比例在90%以上。![]() |
● 锅炉烟气脱硝 |
锅炉烟气脱硝是燃烧烟气中去除氮氧化物的过程,防止环境污染的重要性,已作为世界范围的问题而被尖锐地提了出来。为防止锅炉内煤燃烧后产生过多的NOx污染环境,应对煤进行脱硝处理。分为燃烧前脱硝、燃烧过程脱硝、燃烧后脱硝。世界上比较主流的工艺分为:SCR和SNCR。这两种工艺除了由于SCR使用催化剂导致反应温度比SNCR低外,其他并无太大区别,但如果从建设成本和运行成本两个角度来看,SCR的投入至少是SNCR投入的数倍,甚至10倍不止。![]() |
● 锅炉烟气超低排放 |
2014年9月,国家、环保部、国家联合印发《煤电节能减排升级与改造行动计划》,要求新建机组应同步建设脱硫、脱硝和除尘设施,东部地区新建机组基本达到燃机排放限值,中部地区原则上接近或达到燃机排放限值,鼓励西部地区接近或达到燃机排放限值。同时,稳步推进东部地区现役燃煤发电机组实施大气污染物排放浓度基本达到燃机排放限值的环保改造。 锅炉烟气超低排放,是指火电厂燃煤锅炉在发电运行、末端治理等过程中,采用多种污染物协同脱除集成系统技术,使其大气污染物排放浓度基本符合燃气机组排放限值,即烟尘、二氧化硫、氮氧化物排放浓度分别不超过10 mg/m³、35 mg/m³、50 mg/m³,比《火电厂大气污染物排放标准》中规定的燃煤锅炉地区特别排放限值分别下降50%、30%和50%,是燃煤发电机组清洁生产水平的新。要研发“多污染物协同控制技术”,对燃煤电厂原有的脱硝设备、脱硫设备和除尘设备进行提效改造,并引入新的环保技术对汞和三氧化硫进行进一步脱除,使电厂排放的烟尘、二氧化硫、氮氧化物、汞和三氧化硫达到超低排放的要求。 ![]() |
始终为改善人类生存环境和生活品质而不断努力 |
为中国的资源和环境可持续发展提供全面解决方案和优质服务 |
马上与我们联系,立刻免费获取锅炉烟气净化治理方案 |